Revolutionizing Bronze Casting with Advanced Silicone Mold Solutions
The art of bronze casting, a technique cherished for centuries, hinges on the quality and precision of the molds. As leading manufacturers of silicone rubber, molding silicone, RTV silicone, and RTV2 silicone, we understand the critical role that superior mold-making materials play in producing exceptional bronze sculpture and intricate silicon bronze castings. Our liquid silicone and mold making silicone products are engineered to meet the demanding needs of bronze foundry factories, lost wax casting facilities, and sculpture studios. By partnering with us, you gain access to high-performance materials that enhance the accuracy, efficiency, and profitability of your casting operations.
Why Choose Us?
- Unparalleled Expertise: We possess deep knowledge of casting methods and the challenges faced in the art foundry.
- High-Quality Products: Our silicone molds for metal casting provide exceptional heat resistance, detail reproduction, and durability.
- Customized Solutions: We work closely with you to tailor our silicone to your specific needs.
- Reliable Supply Chain: As a manufacturing plant, we ensure consistent product availability and timely delivery, crucial for your production schedules.
- Technical Support: Our team provides expert guidance on best practices for using our products, maximizing your success in each cast bronze project.
Mastering Detail Reproduction with Silicone in Bronze Casting
Precision is paramount when you make a bronze sculpture or casting. Our silicone products excel at capturing the finest details from your original models. In the lost wax casting process, a wax pattern is the crucial first step. You may use our silicone rubber to create a highly accurate mold for your wax pattern by learning from our guide on Silicone for resin mold making. This silicone mold captures every nuance, ensuring that the final bronze piece faithfully reflects the artist’s vision. The flexibility of silicone also allows for the easy release of complex wax patterns without damage. This reduces the need for repairs, ensures consistent quality in the casting methods, and minimizes material waste, ultimately improving your bottom line.
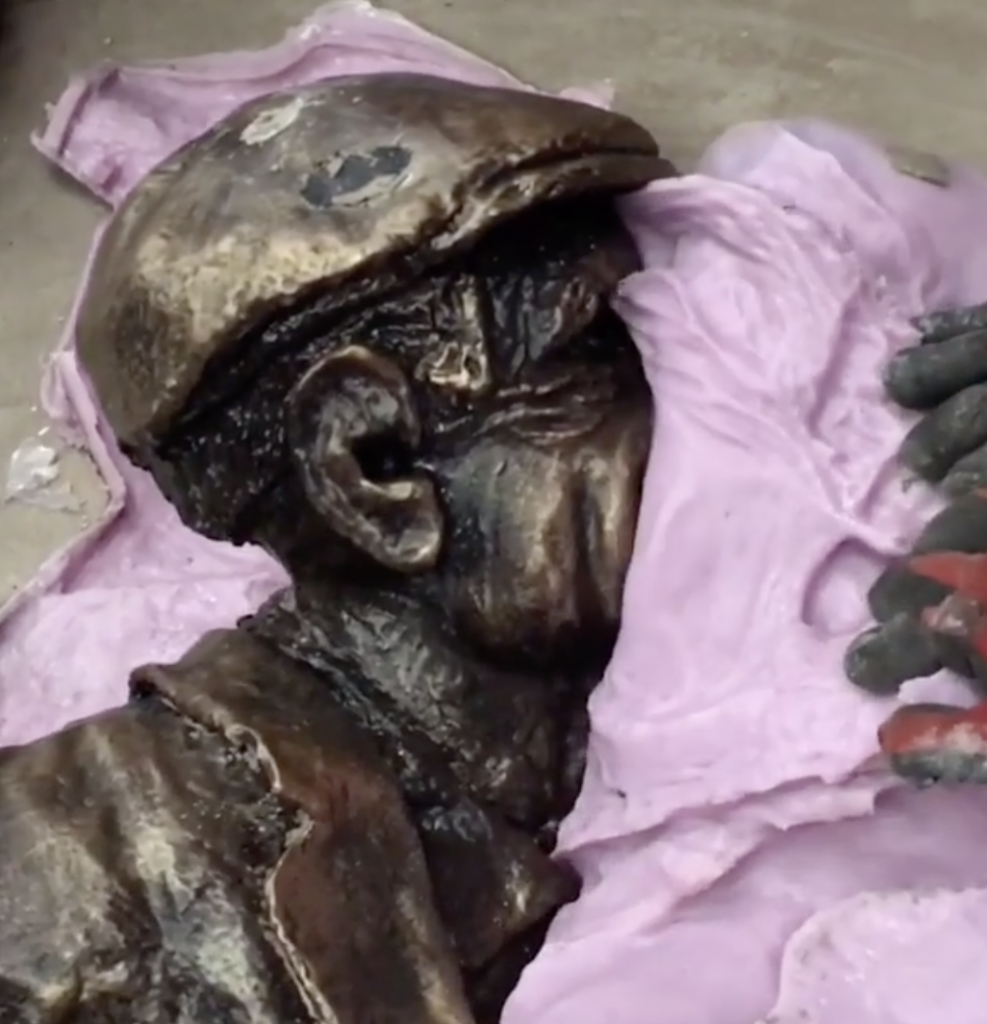
Our RTV2 silicone is particularly well-suited for creating durable molds for various casting methods. This two-part system cures at room temperature, offering a balance of flexibility and strength that can withstand multiple uses. You can confidently pour molten metal into molds made with our RTV2 silicone, knowing that they will maintain their shape and detail integrity throughout the casting process. Our guide on Silicone for Concrete&Stone Molding will teach you some great skills for making a silicone mold, which can bring great results. When the bronze has cooled and solidified, the silicone mold can be easily removed, revealing a flawless cast bronze piece ready for finishing.
H2: Enhancing Durability and Longevity of Silicone Molds for Bronze Casting
In a busy foundry environment, the durability of your molds directly impacts productivity and cost-effectiveness. Our silicone products are formulated to withstand the rigors of repeated use in demanding bronze casting applications. They exhibit excellent resistance to tearing, abrasion, and chemical degradation, ensuring that your molds can be used many times without compromising quality. Even silicon bronze, an alloy that includes copper, zinc, and silicon, can be successfully cast using our silicone.
Feature | Benefit |
High Tear Strength | Resists damage during demolding, extending mold life |
Heat Resistance | Withstands the high temperature of molten bronze |
Chemical Stability | Unaffected by release agents or cleaning solutions |
Low Shrinkage | Maintains dimensional accuracy over multiple castings |
The longevity of our topsil silicone molds translates into significant cost savings for your **foundry**. By reducing the frequency of mold replacements, you minimize downtime and material expenses. This increased efficiency allows you to focus on producing more high-quality bronze foundry castings, ultimately boosting your profitability. Our long-lasting P-40 silicone is perfect for your production needs, see our recommendations on Silicone for Rapid Protyping Casting
H2: Optimizing the Casting Process with Silicone: A Step-by-Step Guide
Using our silicone for bronze casting is a straightforward process designed to enhance efficiency and minimize errors. The first step involves preparing the original model, ensuring it is clean and free of any imperfections. Next, a silicone release agent is applied to the model’s surface to facilitate easy demolding later. Our liquid silicone is then mixed according to the recommended ratio and carefully poured over the model, ensuring complete coverage without trapping air bubble.
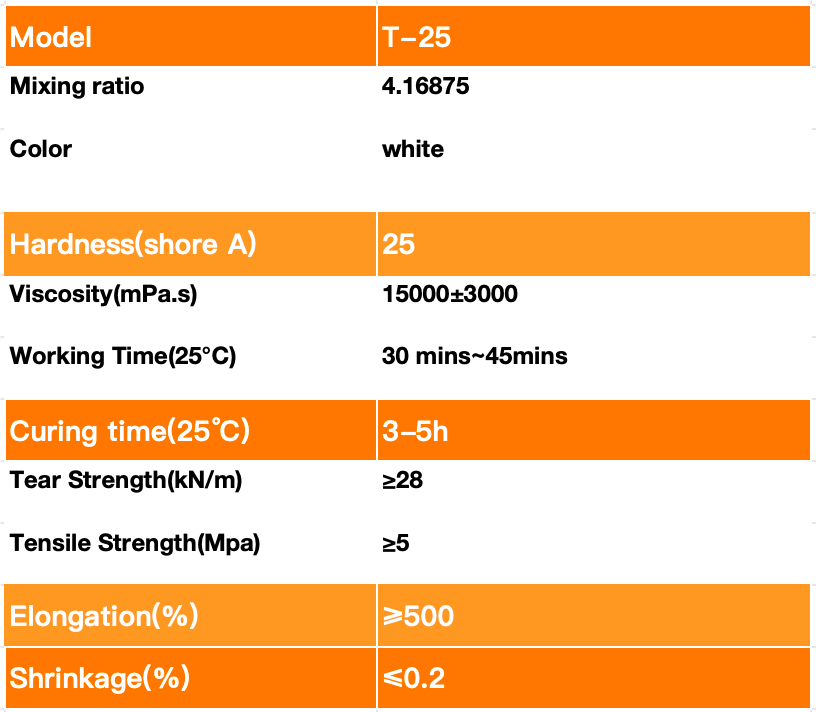
Once the silicone has cured, it forms a flexible yet durable mold that captures every detail of the original. For lost wax casting, wax is then poured into this silicone mold to create a replica of the original model. This wax pattern is then coated with a refractory material, such as ceramic, in multiple layers to form a shell. After the shell hardens, the wax is melted out, leaving a cavity in the shape of the original model. This is similar to the process described in our guide Silicone for GRC/GRG/GFRC Molding, where GRC can also be used as a refractory material. Finally, molten bronze or silicon bronze is poured into the shell mold. The shell is broken away when the metal cools, revealing the finished bronze casting. The silicone rubber can be reused for multiple castings, whether it is cast resin or various metals, making it an excellent choice for producing jewelry, shoes, and more. To create the perfect mold for your shoe, see our guide on Silicone for Shoe Mold Making. For sand castings, the process involves creating a sand mold using a pattern.
“The quality of their silicone has significantly improved our production efficiency and the finish of our bronze sculptures.” – A satisfied customer from a leading art foundry.
We also have a strong commitment to environmental responsibility. Our manufacturing processes are designed to minimize waste, and we prioritize the use of eco-friendly materials. The durability of our silicone molds also contributes to a reduced environmental footprint by extending their lifespan and reducing the need for frequent replacements.
Product Advantages Summary
“Exceptional detail, durability, and ease of use. Our silicone molds have revolutionized our bronze casting process, saving us time and money while delivering superior results.”